Bettering the sustainability of producing includes optimizing total product lifecycles — from materials sourcing and transportation to design, manufacturing, distribution and end-of-life disposal.
In line with the Worldwide Vitality Company, lowering the carbon footprint of business manufacturing by simply 1% may save 90 million tons of CO₂ emissions yearly. That’s equal to taking greater than 20 million gasoline-powered automobiles off the highway annually.
Applied sciences reminiscent of digital twins and accelerated computing are enabling producers to cut back emissions, improve power effectivity and meet the rising demand for environmentally acutely aware manufacturing.
Siemens and NVIDIA are on the forefront of growing applied sciences that assist clients obtain their sustainability objectives and enhance manufacturing processes.
Key Challenges in Sustainable Manufacturing
Balancing sustainability with enterprise goals like profitability stays a prime concern for producers. A research by Ernst & Younger in 2022 discovered that digital twins can scale back development prices by as much as 35%, underscoring the shut hyperlink between useful resource consumption and development bills.
But, one of many greatest challenges in driving sustainable manufacturing and lowering overhead is the presence of silos between departments, totally different vegetation inside the identical group and throughout manufacturing groups. These silos come up from a wide range of points, together with conflicting priorities and incentives, an absence of widespread energy-efficiency metrics and language, and the necessity for brand spanking new expertise and options to bridge these gaps.
Knowledge administration additionally presents a hurdle, with many producers struggling to show huge quantities of information into actionable insights — notably these that may impression sustainability objectives.
In line with a case research by The Producer, 1 / 4 of respondents surveyed acknowledged that their information shortcomings negatively impression power effectivity and environmental sustainability, with practically a 3rd reporting that information is siloed to native use circumstances.
Addressing these challenges requires modern approaches that break down boundaries and use information to drive sustainability. Appearing as a central hub for info, digital twin know-how is proving to be an important instrument on this effort.
The Function of Digital Twins in Sustainable Manufacturing
Industrial-scale digital twins constructed on the NVIDIA Omniverse growth platform and Common Scene Description (OpenUSD) are reworking how producers strategy sustainability and scalability.
These applied sciences energy digital twins that take engineering information from varied sources and contextualize it as it will seem in the actual world. This breaks down info silos and affords a holistic view that may be shared throughout groups — from engineering to gross sales and advertising and marketing.
This enhanced visibility permits engineers and designers to simulate and optimize product designs, facility layouts, power use and manufacturing processes earlier than bodily manufacturing begins. That enables for deeper insights and collaboration by serving to stakeholders make extra knowledgeable selections to enhance effectivity and scale back pricey errors and last-minute modifications that can lead to vital waste.
To additional remodel how merchandise and experiences are designed and manufactured, Siemens is integrating NVIDIA Omniverse Cloud utility programming interfaces into its Siemens Xcelerator platform, beginning with Teamcenter X, its cloud-based product lifecycle administration software program.
These integrations allow Siemens to deliver the facility of photorealistic visualization to advanced engineering information and workflows, permitting corporations to create physics-based digital twins that assist eradicate workflow waste and errors.
Siemens and NVIDIA have demonstrated how corporations like HD Hyundai, a pacesetter in sustainable ship manufacturing, are utilizing these new capabilities to visualise and work together with advanced engineering information at new ranges of scale and constancy.
HD Hyundai is unifying and visualizing advanced engineering initiatives straight inside Teamcenter X.
Physics-based digital twins are additionally being utilized to check and validate robotics and bodily AI earlier than they’re deployed into real-world manufacturing services.
Foxconn, the world’s largest electronics producer, has launched a digital plant that pushes the boundaries of business automation. Foxconn’s digital twin platform, constructed on Omniverse and NVIDIA Isaac, replicates a brand new manufacturing facility within the Guadalajara, Mexico, electronics hub to permit engineers to optimize processes and prepare robots for environment friendly manufacturing of NVIDIA Blackwell programs.
By simulating the manufacturing facility atmosphere, engineers can decide the perfect placement for heavy robotic arms, optimize motion and maximize secure operations whereas strategically positioning hundreds of sensors and video cameras to watch your complete manufacturing course of.
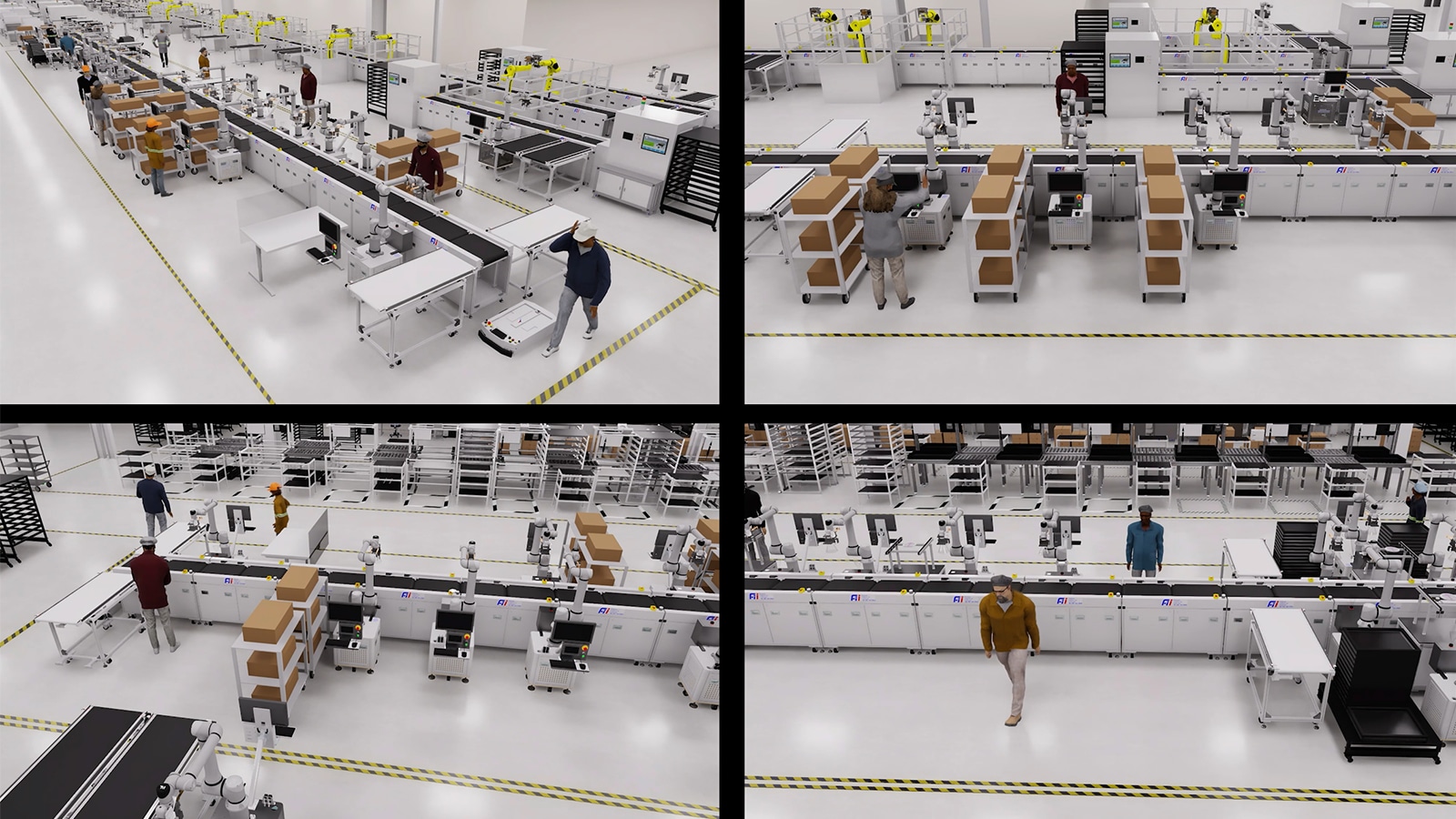
The usage of digital twins, like these in Foxconn’s digital manufacturing facility, is turning into more and more widespread in industrial settings for simulation and testing.
Foxconn’s chairman, Younger Liu, highlighted how the digital twin will result in enhanced automation and effectivity, leading to vital financial savings in time, price and power. The corporate expects to extend manufacturing effectivity whereas lowering power consumption by over 30% yearly.
By connecting information from Siemens Xcelerator software program to its platform constructed on NVIDIA Omniverse and OpenUSD, the digital plant permits Foxconn to design and prepare robots in a practical, simulated atmosphere, revolutionizing its strategy to automation and sustainable manufacturing.
Making Each Watt Rely
One consideration for industries all over the place is how the rising demand for AI is outpacing the adoption of renewable power. This implies enterprise leaders, notably manufacturing plant and information middle operators, should maximize power effectivity and guarantee each watt is utilized successfully to stability decarbonization efforts alongside AI development.
One of the best and easiest technique of optimizing power use is to speed up each potential workload.
Utilizing accelerated computing platforms that combine each GPUs and CPUs, producers can considerably improve computational effectivity.
GPUs, particularly designed for dealing with advanced calculations, can outperform conventional CPU-only programs in AI duties. These programs could be as much as 20x extra power environment friendly in terms of AI inference and coaching.
This leap in effectivity has fueled substantial good points over the previous decade, enabling AI to deal with extra advanced challenges whereas sustaining energy-efficient operations.
Constructing on these advances, companies can additional scale back their environmental impression by adopting key power administration methods. These embody implementing power demand administration and effectivity measures, scaling battery storage for short-duration energy outages, securing renewable power sources for baseload electrical energy, utilizing renewable fuels for backup era and exploring modern concepts like warmth reuse.
Be part of the Siemens and NVIDIA session on the 7X24 Alternate 2024 Fall Convention to find how digital twins and AI are driving sustainable options throughout information facilities.
The Way forward for Sustainable Manufacturing: Industrial Digitalization
The subsequent frontier in manufacturing is the convergence of the digital and bodily worlds in what is called industrial digitalization, or the “industrial metaverse.” Right here, digital twins change into much more immersive and interactive, permitting producers to make data-driven selections sooner than ever.
“We are going to revolutionize how merchandise and experiences are designed, manufactured and serviced,” mentioned Roland Busch, president and CEO of Siemens AG. “On the trail to the economic metaverse, this subsequent era of business software program permits clients to expertise merchandise as they might in the actual world: in context, in beautiful realism and — sooner or later — work together with them by means of pure language enter.”
Main the Approach With Digital Twins and Sustainable Computing
Siemens and NVIDIA’s collaboration showcases the facility of digital twins and accelerated computing for lowering the environmental impression brought on by the manufacturing business yearly. By leveraging superior simulations, AI insights and real-time information, producers can scale back waste and improve power effectivity on their path to decarbonization.
Study extra about how Siemens and NVIDIA are accelerating sustainable manufacturing.
Examine NVIDIA’s sustainable computing efforts and take a look at the energy-efficiency calculator to find potential power and emissions financial savings.